Understanding Blow Moulded Plastic Parts: Processes, Applications, and Benefits
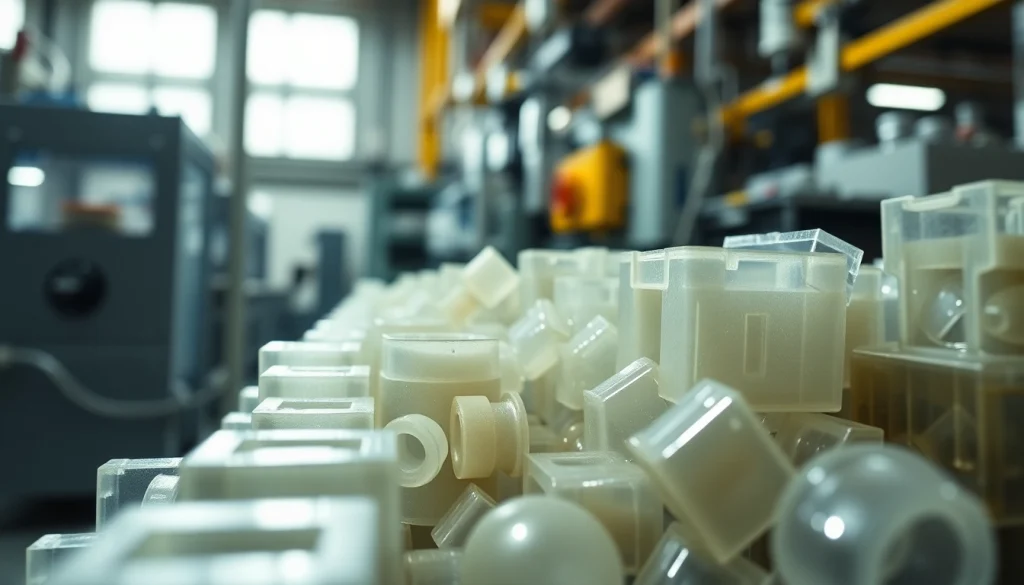
Introduction to Blow Moulded Plastic Parts
In today’s fast-paced industrial world, blow moulded plastic parts have gained significant traction for their utility across various sectors. These parts are not only cost-effective but also exhibit remarkable versatility, making them a preferred choice in manufacturing processes. This section will explore what exactly blow moulded plastic parts are, their inherent benefits, and the wide array of applications in different industries.
What are Blow Moulded Plastic Parts?
Blow-moulded plastic parts are hollow components formed by a manufacturing process known as blow molding. This technique utilizes air to inflate a heated, soft plastic tube called a parison, which is then shaped into a mold to take the desired form. The blow moulding process is particularly known for creating lightweight yet sturdy containers and products, including bottles, containers, and complex parts used in cars and machinery. This method is widely embraced for its ability to optimize material usage and minimize waste, thereby addressing some of the pressing sustainability concerns in manufacturing.
Benefits of Using Blow Moulded Plastic Parts
- Cost-Effectiveness: Blow moulding is highly efficient in terms of both production speed and material utilization, leading to lower manufacturing costs.
- Versatility: The ability to create various shapes and sizes makes blow molding applicable across a multitude of sectors, from packaging to automotive.
- Lightweight and Strong: Products made through blow molding are lightweight without compromising on strength or durability.
- Design Flexibility: Blow moulding allows for intricate designs that can be achieved without additional tooling, unlike traditional manufacturing techniques.
- Sustainability: Many blow-moulded parts can be made from recyclable materials, contributing to a circular economy in manufacturing.
Applications in Various Industries
Blow moulded plastic parts are utilized in a range of industries due to their lightweight and durable nature. Common applications include:
- Packaging: Commonly used for bottles, jars, and containers for food and beverages.
- Automotive: Components like fuel tanks, air ducts, and other vehicle parts are often blow molded for efficiency.
- Consumer Goods: Household products, including toys, bins, and other everyday items.
- Medical Devices: Used in various health-related products where precision and safety are paramount.
The Blow Moulding Process Explained
The blow moulding process is central to creating blow moulded plastic parts. Understanding this process can provide valuable insights into the efficiencies and features of these products. This section will break down the key stages of blow moulding, different techniques employed, and the materials best suited for the process.
Key Stages of Blow Moulding
The blow moulding process consists of several crucial stages, including:
- Heating: The plastic is heated to its melting point where it becomes malleable.
- Forming the Preform: A hollow tube of plastic, known as the parison, is extruded from the heating machine.
- Moulding: The parison is clamped in a pre-designed mold, and compressed air is used to inflate the parison, forcing it to take the shape of the mold.
- Cooling: Once the plastic fills the mold, it is cooled to solidify the material into the desired shape.
- Finishing: The cooled, hollow product is ejected from the mold, and any required finishing touches, such as trimming, can be applied.
Types of Blow Moulding Processes
Blow molding can be categorized into three primary types, each suitable for different applications:
- Extrusion Blow Moulding (EBM): This is the most common method where the parison is extruded into the mold. EBM is widely used for making bottles and containers.
- Injection Blow Moulding (IBM): Here, a preform is created through injection molding, and then it is expanded inside the mold. This method is often used for producing small, precise products.
- Injection Stretch Blow Moulding (ISBM): This process combines the injection and stretch techniques to create bottles with enhanced clarity and mechanical properties, commonly used in beverage industries.
Material Selection for Blow Moulding
Choosing the right materials is vital for the success of the blow moulding process. Common materials include:
- Polyethylene (PE): Known for its excellent strength-to-weight ratio, it is widely used for various containers.
- Polypropylene (PP): Offers high temperature resistance, which makes it suitable for a variety of applications.
- Polyethylene Terephthalate (PET): Renowned in the beverage industry due to its clarity and strength.
- Polyvinyl Chloride (PVC): Used for products requiring durability and high strength.
- Recyclable Materials: Increased focus on sustainability has led to the use of recycled plastics in blow moulding.
Comparing Blow Moulding to Other Manufacturing Techniques
While blow moulding offers numerous advantages, it’s essential to compare it to other manufacturing techniques to understand its unique strengths. This section will discuss how blow moulding contrasts with injection moulding, rotational moulding, and the cost implications of each method.
Blow Moulding vs. Injection Moulding
Blow moulding and injection moulding are two distinct processes used for different types of plastic products:
- Shape and Structure: While blow moulding creates hollow parts, injection moulding is used to produce solid shapes with higher dimensional accuracy.
- Cycle Time: Blow moulding tends to have shorter cycle times for hollow products, making it more efficient for high-volume production.
- Material Usage: Injection moulding generally requires more material due to its solid structure, while blow moulding can be more material-efficient.
Advantages of Blow Moulding over Rotational Moulding
Blow moulding has several advantages compared to rotational moulding, particularly regarding:
- Production Speed: Blow moulding typically achieves faster cycle times compared to the longer processes involved in rotational moulding.
- Material Efficiency: The waste produced during blow moulding can be lower than that in rotational moulding.
- Cost: Blow moulding setups often have lower initial capital costs compared to rotational moulding.
Cost Considerations in Manufacturing
When choosing between manufacturing methods, costs play an important role. The factors to consider include:
- Initial Setup Costs: Blow moulding can have a lower setup cost due to simpler mold construction compared to injection moulding.
- Material Costs: The choice of materials also dictates costs, with certain plastics being more affordable than others.
- Volume Production: Blow moulding becomes more cost-effective as production volumes increase, capitalizing on its efficiency for large-scale manufacturing.
Quality Control in Blow Moulded Plastic Parts Production
Quality control is a critical aspect of manufacturing blow-moulded plastic parts. Ensuring consistency and a high-quality standard is imperative for maintaining market competitiveness. This section explores the essential quality control measures applied in the production of blow moulded plastic parts, addressing common defects, and performance metrics for quality assessment.
Ensuring Consistency and Quality
Implementing a rigorous quality control system helps manufacturers catch defects and maintain product consistency:
- Regular Inspections: Frequent checks during production can help identify inconsistencies in the manufacturing process.
- Standard Operating Procedures (SOPs): Establishing clear SOPs ensures every production step is executed consistently.
- User Feedback: Gathering feedback from end-users can help identify product issues that may not be apparent during manufacturing inspections.
Common Defects and Their Solutions
Even with strict quality controls, defects can occur. Understanding common defects and potential solutions is vital:
- Insufficient Wall Thickness: This can occur due to uneven material flow. Solutions include optimizing the mould design and ensuring consistent material heating.
- Surface Defects: Imperfections on the surface can result from contamination or incorrect mould temperature. Regular cleaning and maintaining optimal mould temperatures can mitigate these issues.
- Blow Moulding Joint Separation: Proper alignment of the mould halves and ensuring adequate clamping pressure can resolve separation issues.
Performance Metrics for Quality Assessment
To assess the quality of blow-moulded products, various performance metrics can be tracked:
- Tensile Strength: Measuring how much pulling force the material can withstand before breaking.
- Impact Resistance: Evaluating how well a product can absorb shocks without breaking.
- Dimensional Accuracy: Ensuring the finished product adheres closely to the intended design specifications.
The Future of Blow Moulded Plastic Parts
The blow moulding industry is on the cusp of several innovations aimed at enhancing efficiency and sustainability. This section will explore what the future holds for blow moulded plastic parts, including technological advancements, sustainability efforts, and market trends.
Innovations in Blow Moulding Technology
Technological innovation is reshaping the landscape of blow moulding:
- Automation: The advent of advanced robotics and automation technologies is boosting productivity and precision in blow moulding operations.
- 3D Printing: Integrating 3D printing in the blow moulding process allows for rapid prototyping and parts customization.
- Smart Manufacturing: IoT-enabled sensors can monitor production in real time, allowing for adaptive manufacturing processes and immediate troubleshooting.
Sustainability and Recycling in Blow Moulding
As global sustainability concerns intensify, blow moulding manufacturers are focusing on greener practices:
- Recyclable Materials: Increasing use of recyclable plastics and resins reflects a commitment to environmental responsibility.
- Energy Efficiency: Advanced technologies are enhancing energy efficiency during production, reducing overall carbon footprints.
- Waste Reduction: Innovations aimed at minimizing material waste during production processes align with sustainability goals.
Market Trends and Consumer Preferences
Consumer preferences are evolving, driven by sustainability and convenience:
- Demand for Eco-Friendly Products: Consumers increasingly prefer products made from sustainable materials.
- Customizable Solutions: The trend towards personalization and customization is leading manufacturers to explore more flexible blow moulding solutions.
- Growth in E-commerce Packaging: The surge in online shopping is driving demand for innovative and efficient packaging solutions, enhancing the prospects for blow moulded plastic parts.