Comprehensive Guide to Blow Moulded Plastic Parts: Insights and Applications
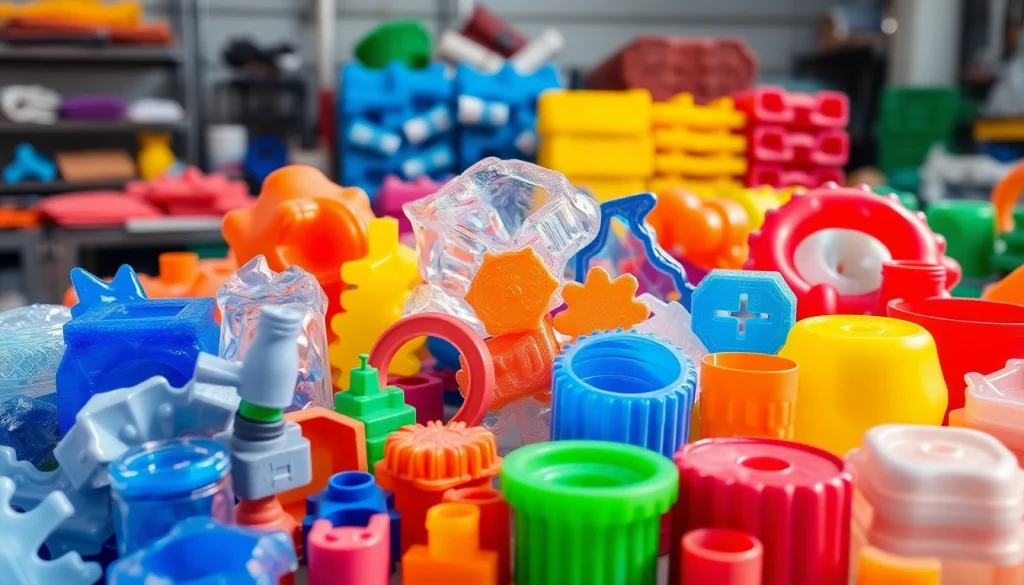
Understanding Blow Moulded Plastic Parts
Introduction to Blow Moulding Process
Blow moulding is a sophisticated manufacturing process utilized extensively in the production of hollow plastic parts, offering an effective solution for various applications from packaging to automotive components. The technique utilizes air pressure to inflate a heated plastic parison into a mold, resulting in a precise and uniform hollow part. This methodology plays a critical role in the production of blow moulded plastic parts, known for their structural integrity and versatility.
Common Applications of Blow Moulded Parts
Blow moulded plastic parts serve numerous industries with unique demands. Some of the most common applications include:
- Packaging: From water bottles to containers, blow moulded parts dominate the consumer market, providing lightweight and durable packaging solutions.
- Automotive Components: Many automotive parts, such as fuel tanks and air ducts, are produced using blow moulding technologies, ensuring both lightweight and high-strength characteristics.
- Consumer Goods: Items such as toys and household products often utilize blow moulding due to the cost-effectiveness and design flexibility it offers.
Benefits of Using Blow Moulded Plastic Parts
The advantages of employing blow moulded plastic parts encompass a broad spectrum:
- Efficiency: Blow moulding allows for rapid production cycles, making it ideal for intricate designs at scale.
- Cost-Effectiveness: High-volume production typically offers reduced costs per unit, benefiting manufacturers and consumers alike.
- Design Flexibility: The process accommodates various shapes without significant changes in tooling, providing adaptability in design evolution.
- Material Efficiency: Minimizing material waste when creating hollow parts enhances sustainability and reduces costs.
Materials Used in Blow Moulding
Types of Plastics Effective for Blow Moulding
The selection of materials is pivotal in the blow moulding process, as different plastics can significantly affect the properties of the final product. Common plastics used in blow moulding include:
- Polyethylene (PE): This versatile plastic is prevalent in blow moulding due to its robustness, chemical resistance, and affordability.
- Polypropylene (PP): Known for its high melting point and high tensile strength, PP is ideal for more specialized applications.
- Polyethylene Terephthalate (PET): Often used in beverage bottles, PET’s transparency and toughness make it a popular choice for consumer products.
- Polyvinyl Chloride (PVC): Its durability and adaptability in various environments allow PVC to be widely used, especially in the construction sector.
Advantages of Different Plastic Resins
The selection of a specific resin can greatly impact several characteristics such as strength, weight, and thermal resistance:
- Durability: Certain resins can enhance the resilience of the product against physical stress.
- Cost Performance: Opting for more affordable resins can cut manufacturing costs without compromising quality.
- Environmental Impact: Biodegradable options and recycled materials are gaining traction in the market, responding to consumer demand for sustainable products.
Impact of Material Selection on Product Quality
The choice of material directly influences the overall quality and performance of the finished blow moulded part. Factors such as thermal properties, clarity, surface finish, and applicability in specific environments must be meticulously assessed to ensure optimal product performance. Poor material choice can lead to defects, poor performance under stress, and ultimately, customer dissatisfaction.
Blow Moulding Techniques Explained
Extrusion Blow Moulding Process
Extrusion blow moulding (EBM) is among the most widely used blow moulding methods. The process involves:
- Heating and extruding a resin to form a parison.
- Positioning the parison in a two-part mold.
- Injecting air to expand the parison against the mold cavity, creating the final shape.
This technique is particularly useful for producing large hollow objects such as tanks and containers.
Injection Blow Moulding Process
Injection blow moulding (IBM) combines injection moulding and blow moulding for accurate part production. The process entails:
- Injecting molten resin into a mold to create a preform.
- Transferring the preform into a blow mould.
- Expanding the preform to form the final part.
This method allows for tighter tolerances and is often used for smaller, more complex parts.
Comparison of Techniques: Pros and Cons
Understanding the strengths and weaknesses of each blow moulding technique is essential for manufacturers:
Technique | Pros | Cons |
---|---|---|
Extrusion Blow Moulding | Low cost, ideal for large parts, fast production speed. | Less precision compared to injection methods, limited to simpler shapes. |
Injection Blow Moulding | Higher precision, better surface finish, suitable for smaller parts. | Higher initial costs, slower cycle times. |
Industry Applications and Case Studies
Packaging: The Role of Blow Moulding
In the packaging industry, blow moulded plastic parts play an essential role by allowing lightweight and cost-effective packaging solutions for various products. For example, beverage manufacturers rely on blow moulded PET bottles due to their clarity and strength, enhancing brand visibility while ensuring product integrity.
Automotive Industry Innovations
The automotive sector employs blow moulding extensively for producing components with high durability, such as fenders and instrument panels. This not only reduces the vehicle’s weight, allowing for enhanced fuel efficiency, but also simplifies complex assemblies by integrating multiple components into a single part.
Consumer Products Made with Blow Moulding
Everyday consumer products, from children’s toys to storage containers, are increasingly being made using blow moulding processes. One notable case is the production of ergonomic water bottles that not only meet fitness and health industry standards but also appeal to environmentally conscious consumers through innovative design and material use.
Why Choose Blow Moulded Plastic Parts?
Cost Efficiency and Production Benefits
Cost efficiency is often one of the driving factors behind the popularity of blow moulded plastic parts. The ability to produce hollow parts with minimal material waste significantly decreases the overall cost of production. Moreover, the speed of the manufacturing process allows for large volumes of products to be produced in a shorter time frame, ensuring that businesses can meet rising customer demands effectively.
Environmental Considerations in Blow Moulding
In recent years, the environmental footprint of manufacturing processes has garnered considerable attention. Blow moulding is no exception; manufacturers are increasingly opting for recyclable materials and implementing energy-efficient practices. Innovations in biodegradable resins also reflect a shift towards sustainability, allowing the industry to align with environmental laws and consumer expectations.
Future Trends in Blow Moulding Technology
The landscape of blow moulding technology is evolving rapidly, driven by advancements in materials science and manufacturing technologies. Future trends may include:
- 3D Printing Integration: Integrating 3D printing technology with traditional blow moulding could lead to rapid prototyping and customization capabilities.
- Smart Manufacturing: Incorporating IoT to monitor and optimize the production process could enhance efficiency and reduce waste.
- Advanced Materials: Continuous research into new polymer blends will allow for enhanced mechanical properties and lower environmental impact.